Für das Schleifen von Keramik, Hartmetall und gehärtetem Stahl werden Schleifscheiben aus hochharten Schneidstoffen wie Diamant oder CBN eingesetzt. Um eine erhöhte Präzision und Wirtschaftlichkeit beim Schleifprozess zu erreichen, ist der Einsatz von Schleifscheiben mit gesinterter Metallbindung wünschenswert.
WireDress® - Die revolutionäre Abrichteinheit
Ihr Einsatz ist jedoch bisher nur bedingt sinnvoll, da sich Metallbindungen nur sehr eingeschränkt und aufwendig abrichten lassen. Eine Möglichkeit und in der Praxis auch eine sehr gängige Methode solche Schleifscheiben abzurichten, ist der Gebrauch von externen Arbeitsmaschinen. Durch die Verwendung solcher externen Arbeitsmaschinen werden jedoch Handlings und Logistikschritte nötig, die den Schleifprozess unterbrechen und dadurch den Betreibern solcher Anlagen unnötige Mehrkosten entstehen lassen. Aus diesem Grund ist bis dato das Abrichten komplexer bzw. feingliedriger Profile wirtschaftlich nicht vernünftig darstellbar.
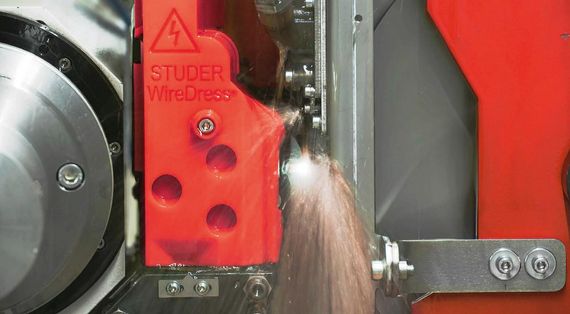
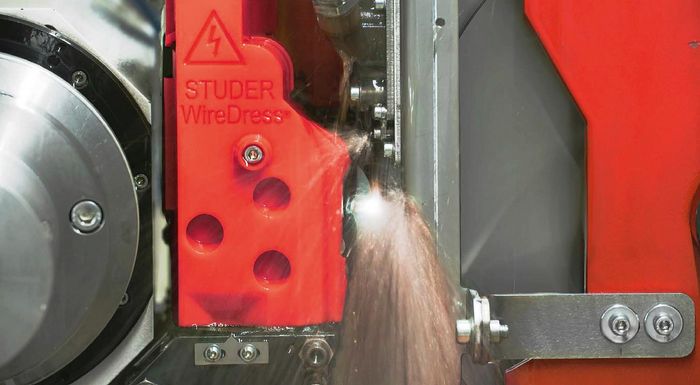
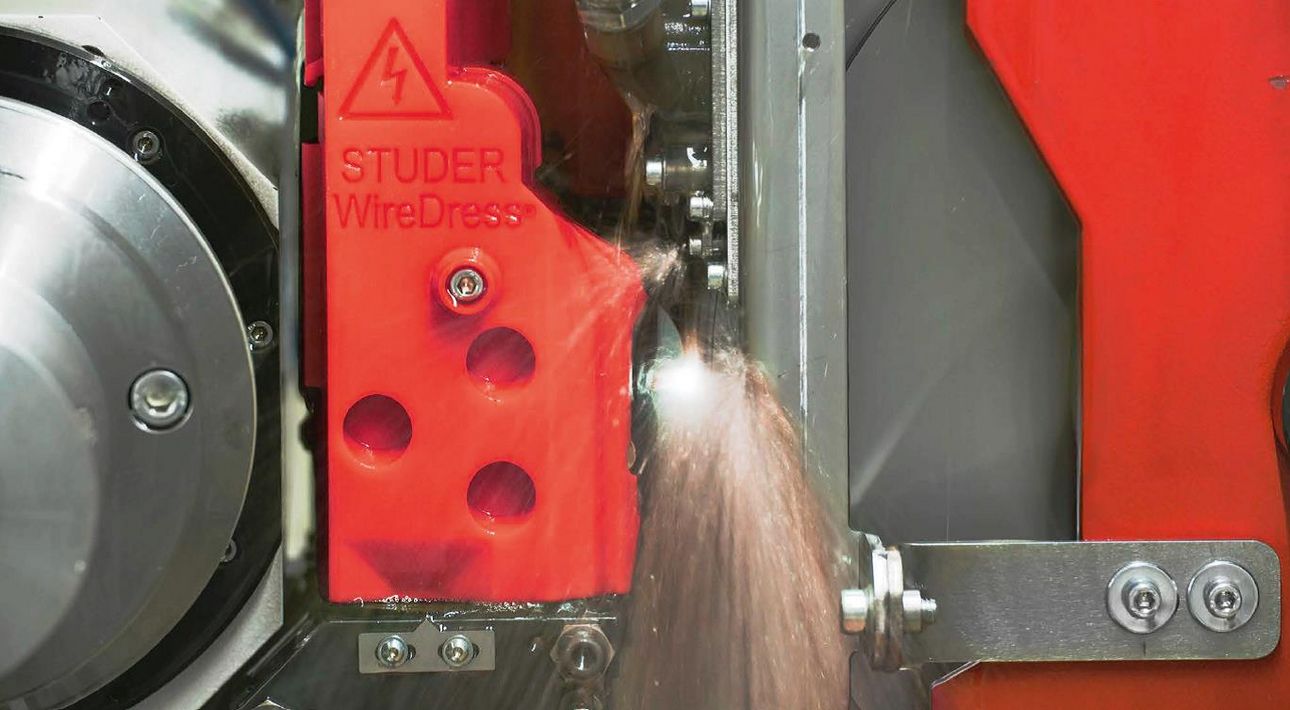
Die Fritz Studer AG, gegründet 1912, ist einer der Markt- und Technologieleader im Universal-, Aussen-, Innenrund- sowie im Unrundschleifen. STUDER steht mit rund 23'000 ausgelieferten Anlagen seit Jahrzehnten für Präzision, Qualität und Langlebigkeit. Mit einer massgeschneiderten Komplettlösung für jede Schleifaufgabe erhält der Kunde das Wissen und Können rund um den Schleifprozess mitgeliefert. Das STUDER Logo gilt weltweit seit Jahrzehnten als Gütesiegel für erstklassige Ergebnisse. Das dies auch in Zukunft gewährleistet ist, arbeitet die Fritz Studer AG kontinuierlich an neuen Innovationen rund ums Schleifen. So hat sich STUDER zur Aufgabe gemacht, eine Abrichteinheit zu entwickeln, welche das Abrichten metallgebundener Schleifscheiben in der Schleifmaschine ermöglicht. Somit entfallen die externen Handlingsschritte sowie Logistikaufgaben für den Anlagenbetreiber und ein wirtschaftliches Abrichten metallgebundener Schleifscheiben wird möglich.
Eine der grössten Herausforderungen war die Integration der neu zu entwickelnden Abrichteinheit in dem zur Verfügung stehenden Arbeitsraum der fertigen Serienschleifmaschinen. Das heisst, die Abrichteinheit muss in die bereits beim Kunden stehenden Anlagen integrierbar sein. Aufgrund des Funktionsprinzips der Abrichteinheit, welche einer kleinen Drahterodiermaschine ähnelt, müssen die Komponenten aus nichtleitenden Materialien gefertigt werden. Zugleich müssen die zu entwickelnden Komponenten eine erhöhte Festigkeit sowie Schutz gegen mechanischen und chemischen Verschleiss aufweisen.
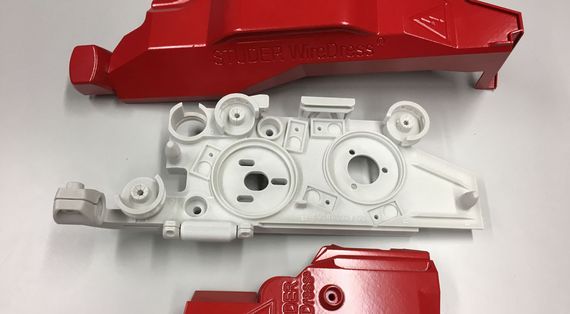
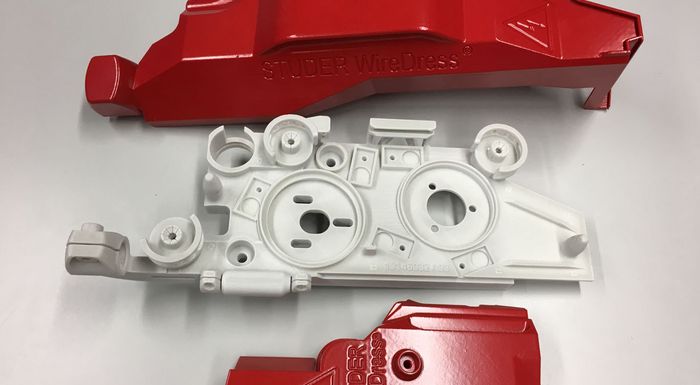
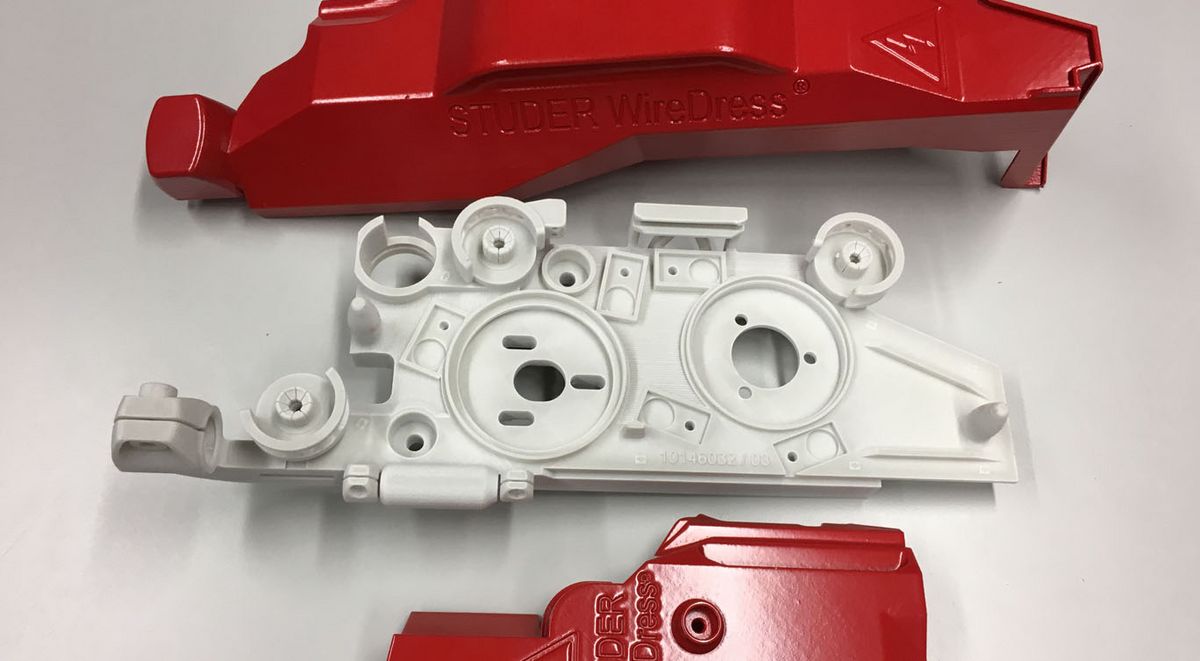
Zu Beginn wurde versucht die Einheit auf konventionelle Weise zu fertigen. Schnell wurde klar, dass eine Umsetzung aller Funktionen mit einem konventionellen Design in dem zur Verfügung stehenden Raum nicht darstellbar ist. Der Platz war schlichtweg zu klein. Ein neuer Ansatz musste gefunden werden. Zusammen mit der Irpd AG, dem Kompetenzzentrum für Additive Manufacturing (AM) der UNITED GRINDING Group, konnten die Konstrukteure die Stärken des Additive Manufacturing – im Speziellen das Selective Laser Sintering (SLS) – nutzen und in Ihr neues Design mit einfliessen lassen. Durch den Einsatz dieser Technologie eröffneten sich zahlreiche neue Möglichkeiten hinsichtlich Designfreiheit oder auch Funktionsintegration. Ein deutlich schlankeres Design der kompletten Baugruppe konnte realisiert werden. Bereits während der Entwicklungsphase konnten die kurzen Lieferzeiten der SLS-Komponenten bei Bauteiländerungen überzeugen und Wettbewerbsvorteile generieren. Nahezu alle Komponenten der Abrichteinheit sind additiv in Kunststoff gefertigt.
Konstruktive Herausforderung und Freiheiten
Eine der grössten Herausforderungen für die Konstrukteure war sicherlich das Umdenken, sowie die zu einem konventionell designten Bauteil differenzierte Herangehensweise in der Konstruktion welche mit einem additiv gerechten Design einhergehen. Eine AM- gerechte Konstruktion ermöglicht viele neue Möglichkeiten für das spätere Bauteildesign. Um diese Möglichkeiten nutzen zu können, musste ein Umdenken bei den Konstrukteuren stattfinden. Funktionen die bei einem konventionellen Design undenkbar und nicht zu fertigen sind, werden nun möglich. Das Know-how wie ein solches Design aussehen könnte und alle anderen wichtigen Anforderungen die man bei einer AM gerechten Konstruktion einzuhalten hat, wurde bei einem mehrtätigen ThinkAddtive® Workshop bei der Irpd AG vermittelt.
Am Beispiel der Grundplatte aus DuraForm HST lassen sich die Möglichkeiten der additiven Fertigung vor allem in Bezug auf einen sehr hohen Grad an Funktionsintegration aufzeigen. Die Zusammenfassung mehrerer Komponenten zu einem Bauteil trägt signifikant zur Reduktion der erforderlichen Montageaufwände bei. Weiter wurde eine strömungsoptimierte Kühlschmierstoffleitung in der HST-Grundplatte integriert, die den Draht während des Prozesses konstant und gleichmässig benetzt. Die im HST-Material enthaltenen Mineralfasern tragen im Vergleich zum konventionellen Werkstoff PA12 zu einer erheblichen Festigkeitssteigerung bei. Dies ermöglicht die Fertigung von masshaltigen Bauteilen, die sich zugleich durch hohe Festigkeit auszeichnen. Zum Schutz gegen mechanischen und chemischen Verschleiss bzw. zur Sicherstellung einer hohen Bauteilstandzeit erfährt das Bauteil eine spezielle Oberflächenbehandlung.
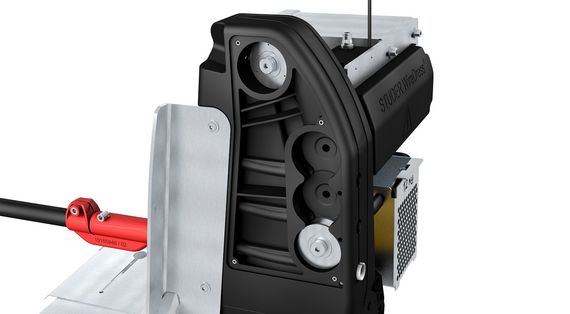
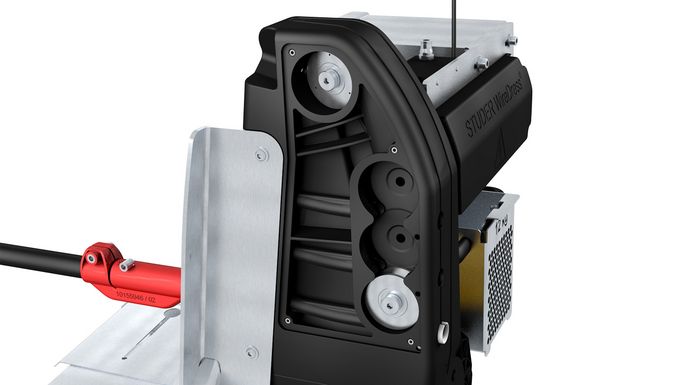
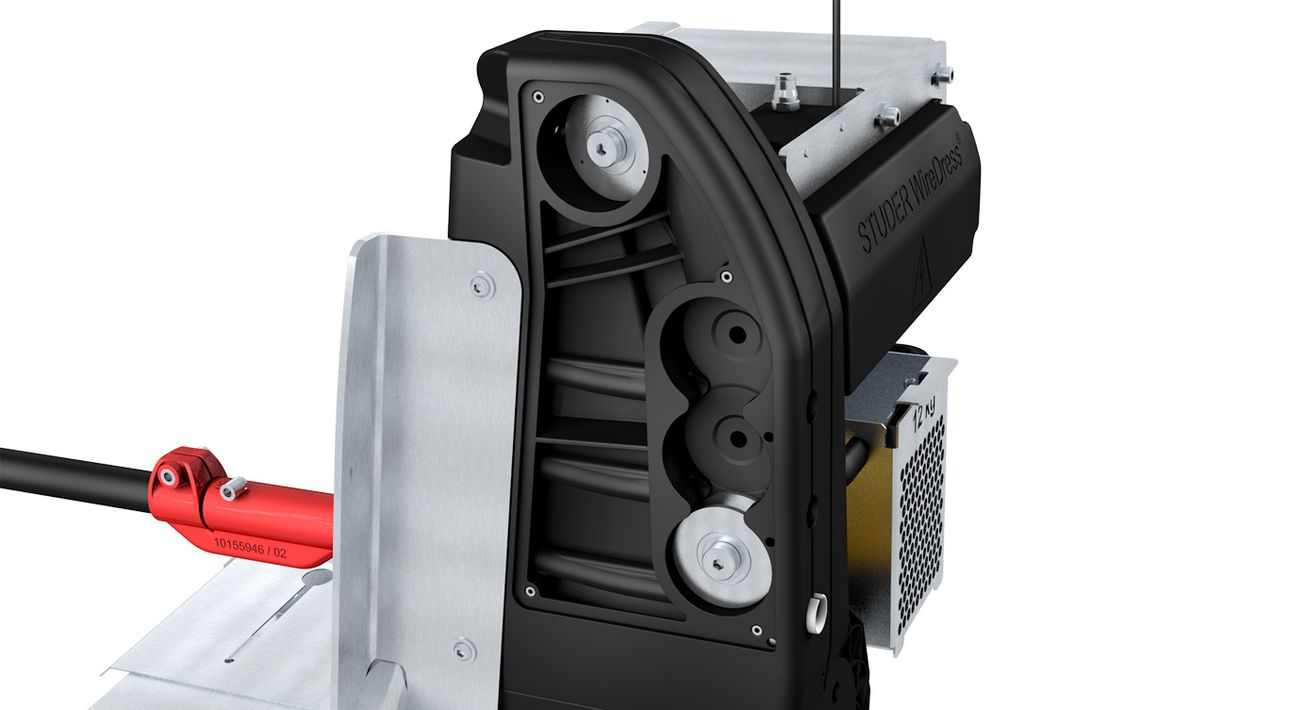
Auch bei den Abdeckungen zum Schutz der verbauten Komponenten, konnten die Stärken der AM- Technologie umgesetzt werden. Die Form der Abdeckung kann perfekt an den Innenraum der Schleifmaschine angepasst werden. Für verschiedene Schleifmaschinen können so einfach die Abdeckungen angepasst werden, ohne dass weitere Komponenten wie z.B. die Grundplatte verändert werden muss. Durch den Einsatz von Wabenstrukturen auf der Innenseite der Abdeckungen, konnte eine hohe Steifigkeit bei sehr dünnen Wandstärken realisiert werden. Auch wichtige Warnhinweissymbole konnten bereits bei der Konstruktion des Bauteils berücksichtigt werden und somit direkt auf der Abdeckung dargestellt werden. Damit entfällt ein nachträgliches Aufkleben der Warnhinweise und verhindert ein entfernen des Warnhinweises bzw. dass dieser durch die nassen Bedingungen in der Schleifmaschine beschädigt werden kann. Zum Schutz des Kunststoffes gegen das Kühlschmiermittel in der Schleifmaschine wird die Oberfläche abschliessend noch versiegelt.
Projekt-Erfolg
Mit dem Einsatz der SLS-Technologie und den damit verbundenen Möglichkeiten eines AM gerechten Design wurde das System STUDER-WireDress® entwickelt, welches in der Rundschleifmaschine und deren Steuerung vollständig integriert ist. Somit entfällt das mühsame Demontieren und Wiedereinstellen der Schleifscheibe bei einer erneuten Montage. Mit dem System hat der Anlagenbediener erstmals die Möglichkeit, Schleifscheiben bei voller Arbeitsgeschwindigkeit in der Anlage abzurichten, d.h. profilieren und schärfen zu lassen. Die Schleifscheibe erhält zudem eine hohe Schnittigkeit mit hohem Kornfreistand. Die Gesamtanlageneffektivität (OEE) konnte deutlich erhöht sowie die Schleifleistung um mehr als 30 % gesteigert werden. Ohne den Einsatz und die Möglichkeiten der SLS Technologie wäre ein positives Gelingen dieses Projektes in dieser Form nicht möglich gewesen. Die SLS Komponenten werden aktuell bereits in Serie hergestellt und befinden sich erfolgreich bei zahlreichen Kunden im Einsatz.